Proceso de Soldadura Continua en Latas
Comienzos
A principios de los años 60 del pasado siglo, se desarrollaron más o menos simultáneamente, dos procesos diferentes de soldadura sin aportar aleación, con fines comerciales, para unir los bordes laterales de los cuerpos de las latas tipo "tres piezas".
Este proceso de soldadura se basa en aportar a las zonas a unir una cantidad de energía en un tiempo determinado. Esta energía se transforma en calor capaz de fundir las partes de metal a soldar. La aportación de energía se hace por medio de una corriente eléctrica y el proceso desencadenado esta muy bien estudiado por las leyes de la Física.
Continental Can introdujo el "Conoweld". Esta técnica se utilizó, inicialmente, para la producción de latas de bebidas de acero con revestimiento electrolítico de cromo (TFS). Para efectuar soldaduras satisfactorias con las primeras máquinas, se requería que la superficie del acero no tuviera revestimiento de cromo en un ancho de unos 2 mm. a cada lado de los bordes que formaban la costura.
Aproximadamente al mismo tiempo Soudronic AG de Suiza, introducía las máquinas semiautomáticas de costura por soldadura eléctrica para hojalata. Estas primeras soldadoras Soudronic se utilizaron en la fabricación de grandes envases metálicos para productos en general. Las costuras laterales se superponían hasta 4,5 mm, produciendo lo que llegó a conocerse como soldadura "Mariposa" (Butterfly) (ver figura mas abajo). Esta soldadura “Batterfly” no valía en envases para alimentos, ya que se comprobó que existían grandes dificultades para barnizar los bordes pronunciados de la costura. El espesor de este tipo de soldadura era tan elevado que no se podía cubrir por medio de una capa de barniz, por muy alta que fuese la carga de este.
Desarrollo de la soldadura WIMA y SUPERWIMA
A mediados de la década de los 60, Soudronic había introducido máquinas totalmente automáticas para la producción de cuerpos de latas de tamaño medio y grande. En 1969, la Compañía introdujo maquinas de más velocidad, para la fabricación de envases aerosol, produciendo 200 unidades por minuto. Sin embargo, tal vez la aportación mas importante tuvo lugar en 1975, con el Sistema de Soldadura por Alambre "Perfilado"(wire mash welding system) (WIMA). Esta técnica comporta la utilización de un alambre de cobre estirado y aplastado, de manera que se aumenta la superficie de contacto en la zona de soldadura, produciendo una soldadura más sólida y adecuada, con una solapa de solo 1 mm de ancho (Bajo Translape.
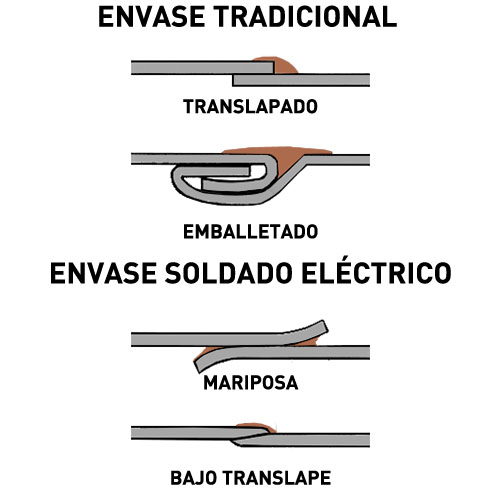
Soudronic desarrolló la utilización del alambre de cobre, como electrodo intermedio entre la costura de la lata y las roldanas de soldadura de cobre, para resolver el problema de la contaminación de la superficie del electrodo, y sus efectos en la calidad de soldadura. Como el alambre no se vuelve a utilizar, la contaminación del electrodo dejó de ser un problema. Por otro lado, el desecho del alambre tiene un alto valor económico. Las roldanas estaban montadas con una inclinación de 2º, para achaflanar ligeramente el borde de la costura y así reducir el escalón y facilitar el rebarnizado de la misma.
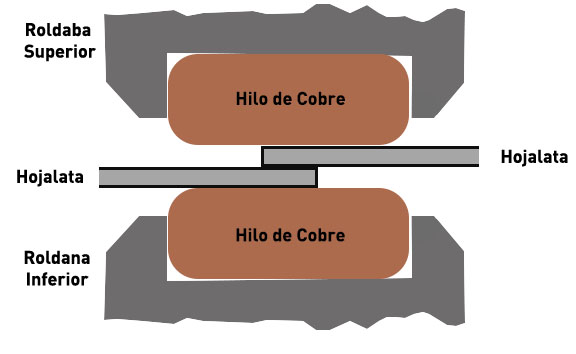
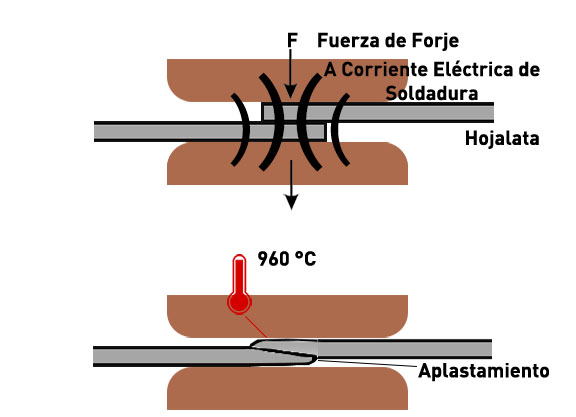
Estas mejoras permitieron a los fabricantes de latas producir botes de unión lateral por soldadura sin aleación para su utilización por vez primera en la industria alimentaría y otras aplicaciones exigentes.
En 1978, se introdujo el Sistema de Soldadura SUPEWIMA. Este desarrollo del proceso de soldadura necesita un solape de sólo 0,15-0,3 mm en la costura lateral. A esta hay que añadir otras ventajas: reducción de la zona de soldadura afectada por el calor; menor endurecimiento, y reducción del grueso de la costura (aproximadamente 1,2 x grosor de la plancha). Junto con una mayor eficacia en el proceso de soldadura, se produjeron mejoras en las velocidades a las que las máquinas podían operar, siendo capaces de producir más de 500 envases por minuto.
El sistema básico de las máquinas de fabricación de cuerpos de Soudronic comprende un sistema de alimentación de cuerpos planos a la máquina, un sistema de desfibrado de los mismos, una unidad de enrollado y la estación de soldadura. En esta última se encuentran los brazos, que soportan las roldadas. En el brazo inferior van incorporados todos el sistema de conductos para las distintas funciones (hilo de cobre, refrigeración, nitrogeno, barniz…).. La máquina productora del cuerpo del bote, puede contar también con una unidad de corte para cuerpos de doble o triple altura, un sistema incorporado para soldar en atmósfera inerte para evitar la formación de óxido, y una unidad de barnizado de costura lateral tanto por la parte interior como por la exterior del cuerpo
El cuerpo del envase una vez formado, es introducido mecánicamente en la estación de soldadura, donde el solape se mantiene constante. La técnica que emplean las soldaduras Soudronic es, simplemente, un procedimiento de soldadura por descargas continúas.
En los procesos WIMA y SUPERWIMA, la temperatura del cuerpo sobrepasa los 900º C. para garantizar una efectiva superación de la fase sólida del metal a lo largo la costura. Sin embargo, ésta es bastante menor que las temperaturas que se alcanzaban con los modelos anteriores.
En el sistema Soudronic se emplea una entrada de corriente alterna sinusoidal. Una máquina de 50 hercios produce 100 descargas (puntos de soldadura) por segundo, y una máquina de 500 hercios produce 1.000 en igual tiempo.
Como ya hemos indicado, la incorporación de una unidad de corte en la máquina soldadora, permite también la soldadura de cuerpos de doble altura. Además esta incorporación, puede incrementar la producción con frecuencias de soldadura mas bajas, o hacer posible la fabricación de cuerpos más cortos, que de otra manera la máquina no podría manejar. Si el envase ha de ser acordonado o entallado, la soldadura se hace en una atmósfera de gas inerte, ya que la misma necesita verse libre de óxido. La formación de una película de oxido seria muy negativa, ya que podría desprenderse en un proceso posterior. El rebarnizado posterior de la zona de soldadura, se lleva a cabo porque el proceso no permite aplicar barniz en hoja plana en la zona de soldadura, ya que dificultaría el paso de la corriente. Este barniz es posteriormente curado dentro de la línea de fabricación.
Soudronic está a la cabeza a nivel mundial, en cuanto al proceso de costura lateral por soldadura eléctrica, con miles de unidades diferentes operando en todo mundo.
Fundamentos de la Soldura Eléctrica
Esquema básico de un punto
Un punto de soldadura se engendra al fundirse el metal por la acción del calor desarrollado por paso de una alta intensidad de corriente a baja diferencia de potencia.
Aunque hay dos tipos de corriente, continua y alterna, sabemos que la de uso normal es la segunda. Se denomina corriente alterna (abreviada CA en español y AC en inglés) a la corriente eléctrica en la que la magnitud y el sentido varían cíclicamente. La forma de onda de la corriente alterna más comúnmente utilizada es la de una onda sinusoidal, puesto que se consigue una transmisión más eficiente de la energía. Para conseguir un elevado número de puntos de soldadura por unidad de tiempo, se aumenta la frecuencia de la corriente alterna empleada. Expliquemos un poco más el proceso.
La corriente alterna a la frecuencia de suministro normal de la red industrial, le llega a la maquina soldadora, que la introduce en un convertidor de frecuencia aumentando por tanto la misma en un numero importante de hercios. Así por ejemplo en un caso concreto se pasa de 50 hercios/segundo – frecuencia de suministro – a 500 hercios/segundo – salida del convertidor-.
La intensidad de corriente en el momento de producirse la soldadura, se mueve entre los valores de 1500 a 2000 amperios y la tensión o diferencia de potencial en torno a 4.5 - 6.5 voltios. Por tanto la corriente eléctrica, convenientemente transformada a estas condiciones de frecuencia, intensidad y voltaje, se hace pasar a través de la estación de soldado, por medio del hilo de cobre perfilado y guiado por las roldadas, actuando sobre el solapamiento de hojalata, para generar un punto de soldadura.
Esquema Básico de una linea continua de puntos de soldadura
Cada hercio produce una sinusoide completa en la grafica de frecuencia, es decir dos puntas inversas y por lo tanto dos puntos de soldadura. Por ello, con una frecuencia de salida de 500 hercios se generan 1000 puntos de soldadura/segundo. Esta sucesión de puntos dan lugar a una soldadura continua a lo largo de la costura lateral de la lata.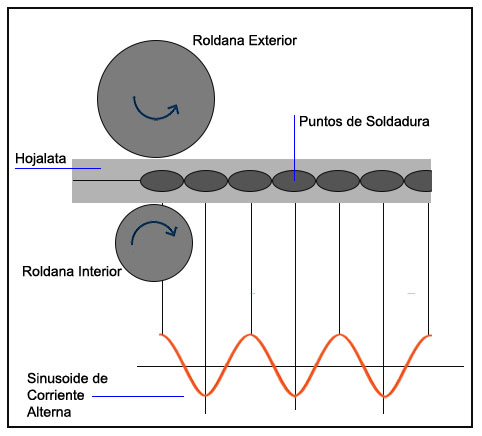